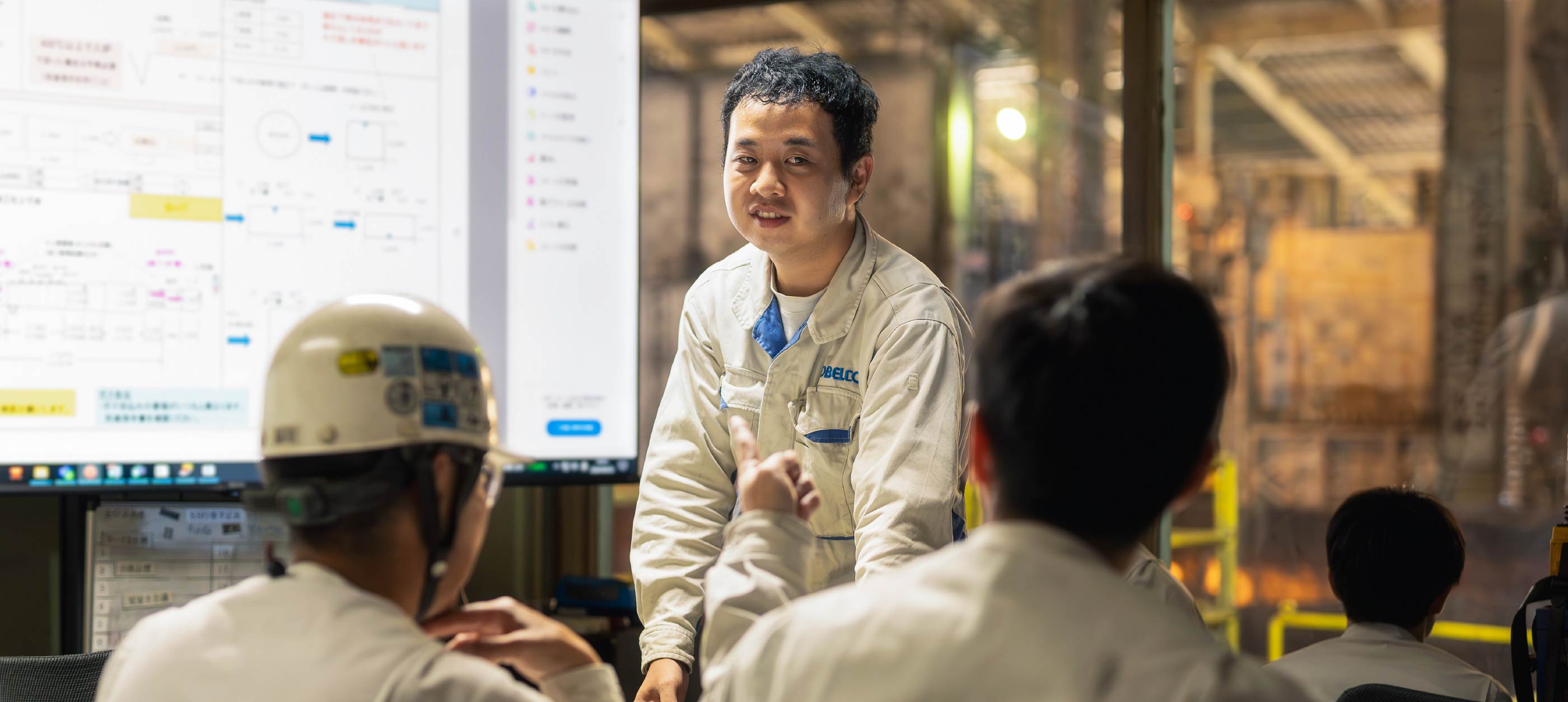
高砂製作所
素形材事業部門 鋳鍛鋼ユニット
鋳鍛鋼工場 製造部鍛圧室
Kさん
2018年新卒入社
工学研究科 マテリアル生産科学専攻 修了
CAREER
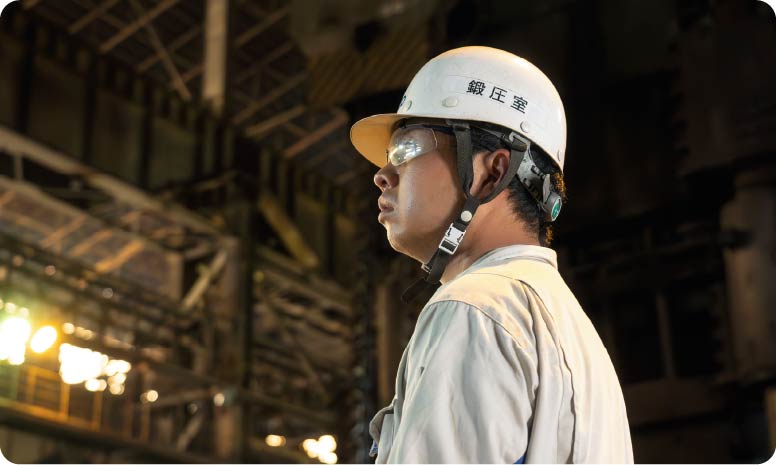
- 2018年
-
新卒入社
鉄鋼事業部門
鋳鍛鋼事業部 鋳鍛鋼工場 鍛圧部 鍛圧技術室 配属
(現・素形材事業部門 鋳鍛鋼ユニット 鋳鍛鋼工場 製造部 鍛圧室)鋳鍛鋼工場で鍛造品の製造コストダウンや変動費削減に携わる。
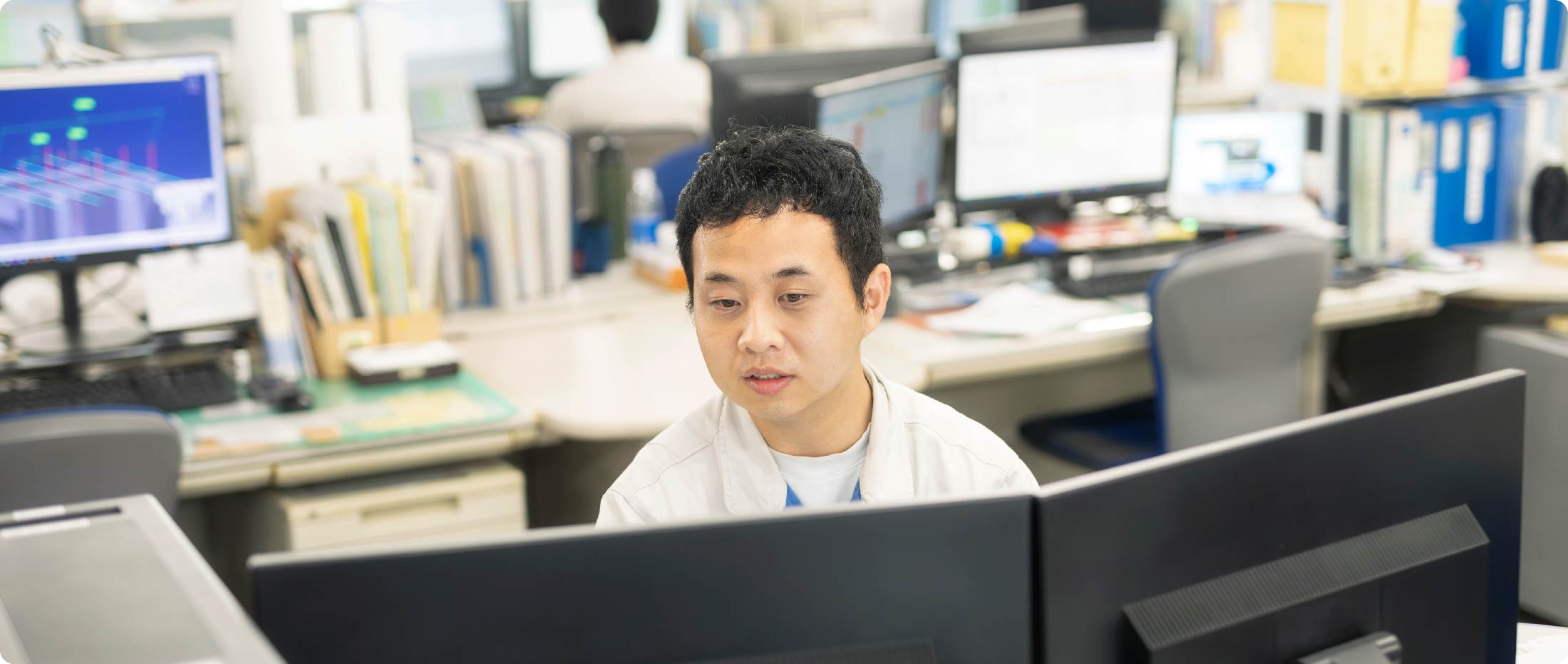
製造コストの3割を占める
主要ラインを最適化する。
目の前で鋼が加熱されて、すごい速度でラインを通っていく。加古川製鉄所の工場を見学したとき、その迫力に目を奪われました。さらに驚いたのは、何百トンという鉄の塊を圧延する際に、数ミリ単位で厚みを制御しているということ。材料関係の会社に就職したいと思っていた私にとって、神戸製鋼の仕事のスケール、技術力の高さは魅力的でした。私が入社後に配属となったのは鋳鍛鋼工場の鍛圧室。製鋼室と加工室の間にあたる鍛圧室は製造の中間工程を担い、製造コストのうち全体の3割ほどを占める工場の主要なライン。主な製品は、船舶用のクランクシャフトで、神戸製鋼が高い世界シェアを誇る製品でもあります。製鋼室から送られてくる鋼塊は、ひと塊、大きいものだと数百トン以上あります。そこから鍛圧室で加熱・鍛造を複数回繰り返し、成型し、その後熱処理を行います。加工室に送るまでで、どれだけ加工しやすいように製品形状・材料特性をつくり込めるかが、鍛圧室の腕の見せ所。私は生産技術スタッフとして、鍛圧室の製造費削減や生産性向上、作業安全性の向上に取り組んでいます。
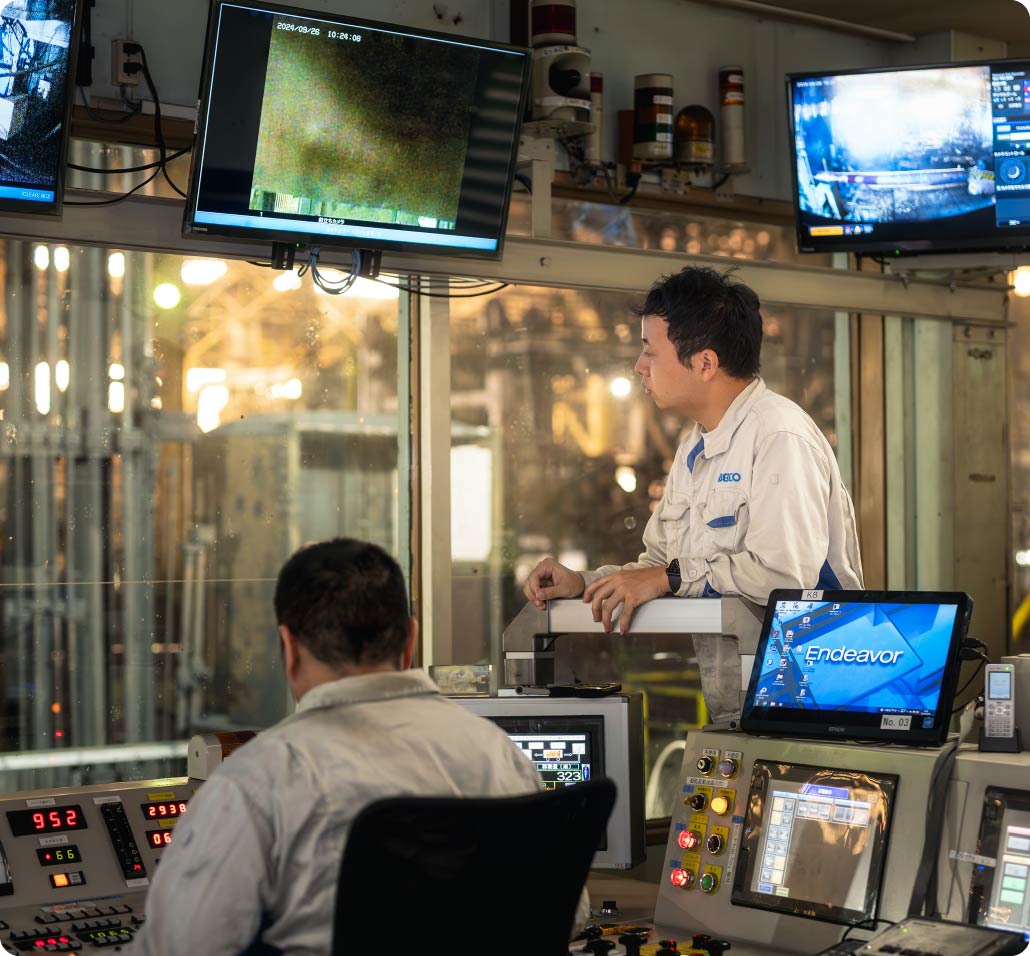
欠陥の原因究明。
仮説の検証を続けた1年。
難しい課題にぶつかっても、「なぜ?」を何度も繰り返し、解決策を考え続ける。その大切さを痛感したのは、一定頻度で発生していた製品内部の欠陥の改善にあたった時のこと。「Kくん、調査してくれる?」上司に声をかけられたのは入社4年目のときでした。当初、内部の欠陥は割れの起点となりやすい化合物によるものだと考えられていました。ところが実際に欠陥のあった製品を切り離して切断面をよく調査したところ、化合物だけに着目しても改善できないことが分かったのです。鍛造時の圧下方法によって製品内部のひずみ分布が変化し、それが割れにつながっているのではないか。その仮説のもと、解決策を探るために、加熱の温度や押し方など、条件を変えて試験を行うことにしました。複数の試験材を取得し、試験を続けること約1年。切断調査を行うのも鍛造方法を工夫するのも、まったく初めての経験。開発室の協力をいただきながら調査を進めていきました。
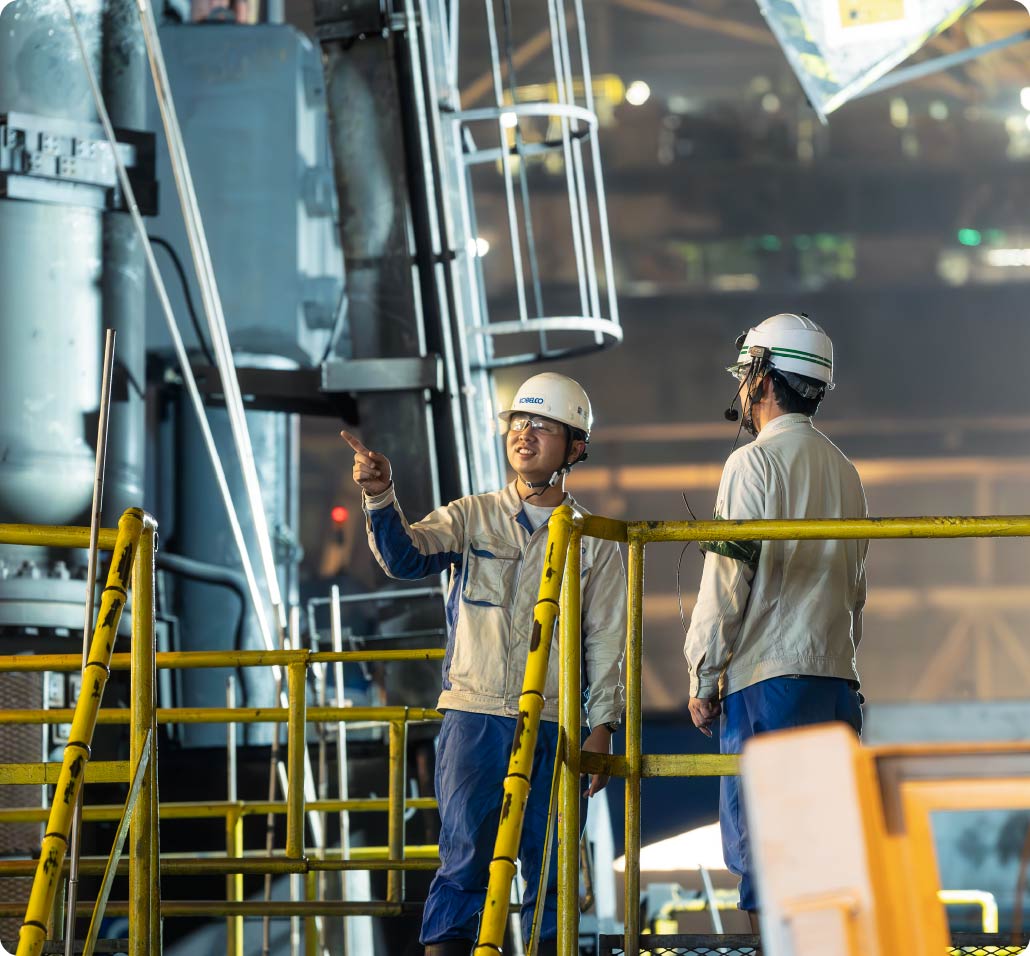
「なぜ?」を考え続ければ、
解決策は必ず見つかる。
答えがないものに対してどうアプローチするか。思えば大学の研究室でも、同様のプロセスで、仮説のもとに実験を繰り返し、「なぜ?」を考え続けていました。大学の研究室と違うのは、私が取り組んでいる改善提案が、工場のコストダウンに直結すること。試験を続けた結果、ようやく割れを防ぐ鍛造方法を解明することができたのです。鍛造方法を工夫したことでコストUPとなっていた対策を廃止し、結果的に大きなコストダウンにつながりました。入社5年目には社内の技術発表会で役員の前でプレゼンする機会もいただき、多くの反響もいただきました。考え続ければ、解決策は必ず見つかる。この時の成功体験を胸に、これからも答えのないテーマに挑んでいきたいと考えています。今後取り組んでみたいのは、作業の自動化や省人化。鋼を1200度で加熱するなどの暑熱作業が多いため、ものづくりの現場は、危険を伴うケースもあります。作業者の災害リスクを低減させるためにも、危険な作業の自動化に取り組んでいきたい。そしていつか、高砂の鍛圧室にKあり。そんなふうに頼っていただける技術者になりたいと思っています。
SCHEDULE
とある1日のスケジュール
- 09:00
-
出社
メールや昨晩の現場からの申し送り内容の確認、操業データの確認を行います。
- 10:00
-
現場での製品対応
製品のキズや形状のチェック、工事進行可否の判断をします。
- 11:00
-
製造指示作成・承認
製品の品質的な懸念事項の検討、指示内容に誤りがないかの確認を行います。
- 12:00
-
昼休憩
- 13:00
-
設備投資案件の推進
見積もり業者との打ち合わせを行います。
- 14:00
-
現場とのミーティング
寸法成績のフィードバックや歩留改善のディスカッションなどを行います。
- 16:30
-
室ミーティング
今週発生した操業、品質、安全などに関する情報を週一で共有します。
- 17:30
-
稟議申請書類作成
安全関係の設備投資の文面推敲、投資によるリスク低減効果の算出をします。
- 18:00
-
退社
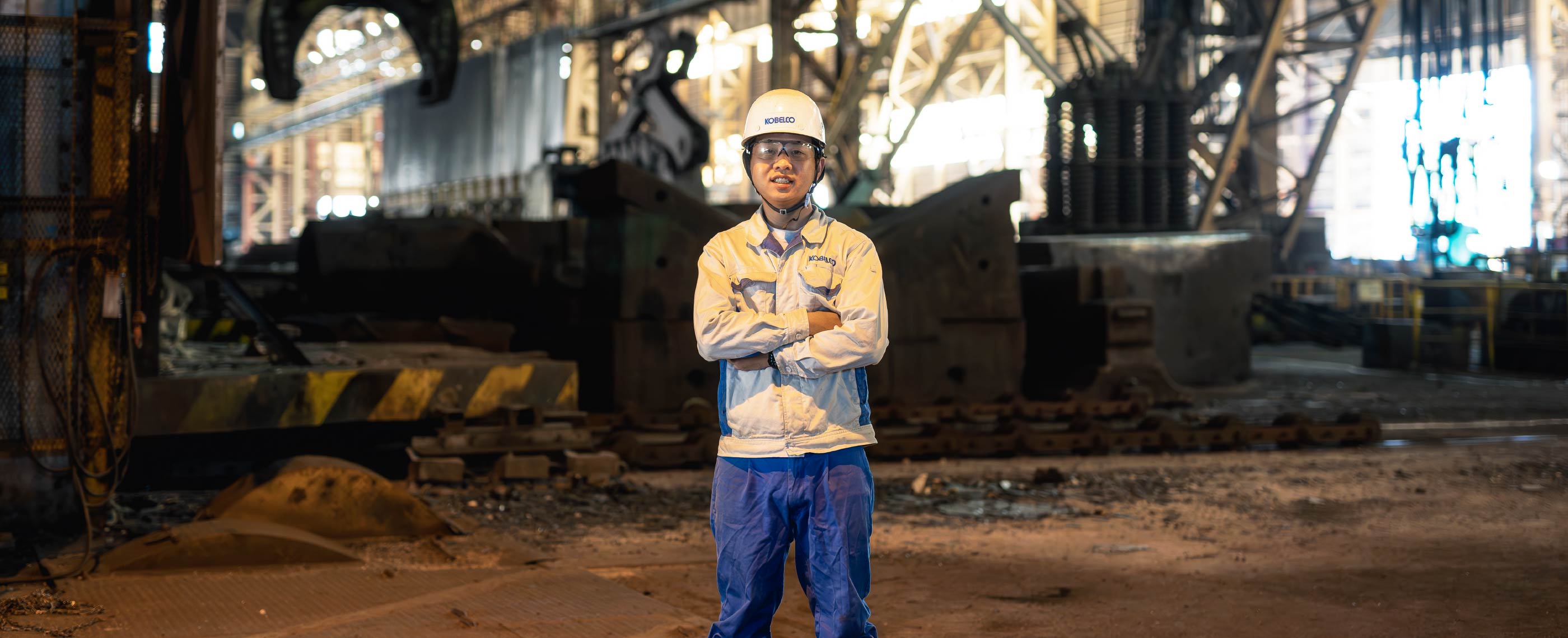